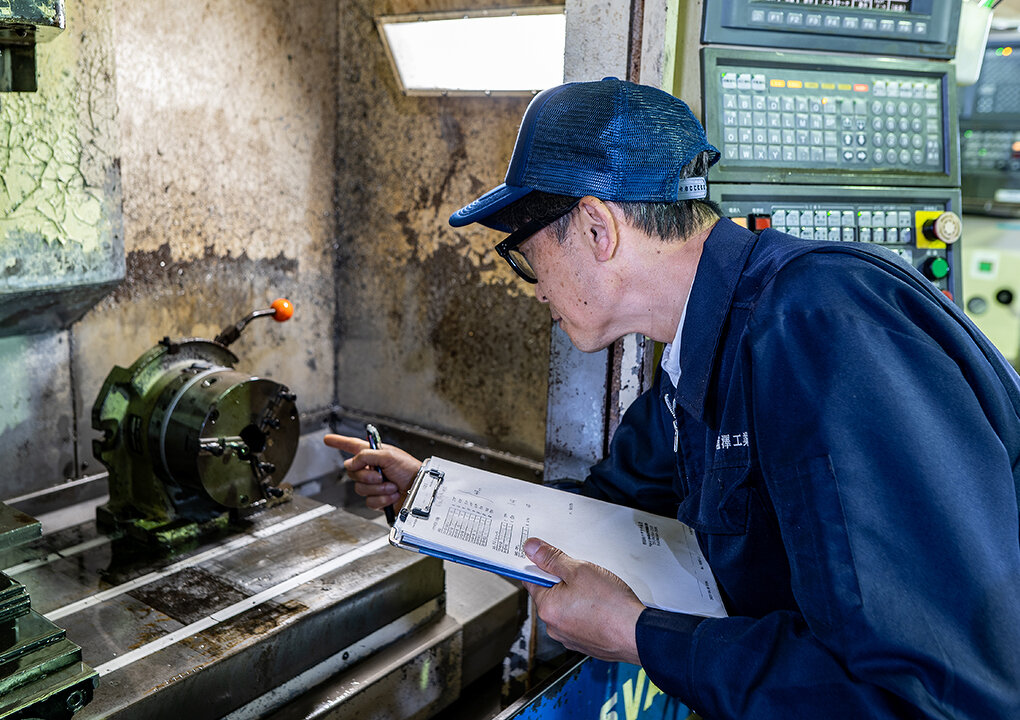
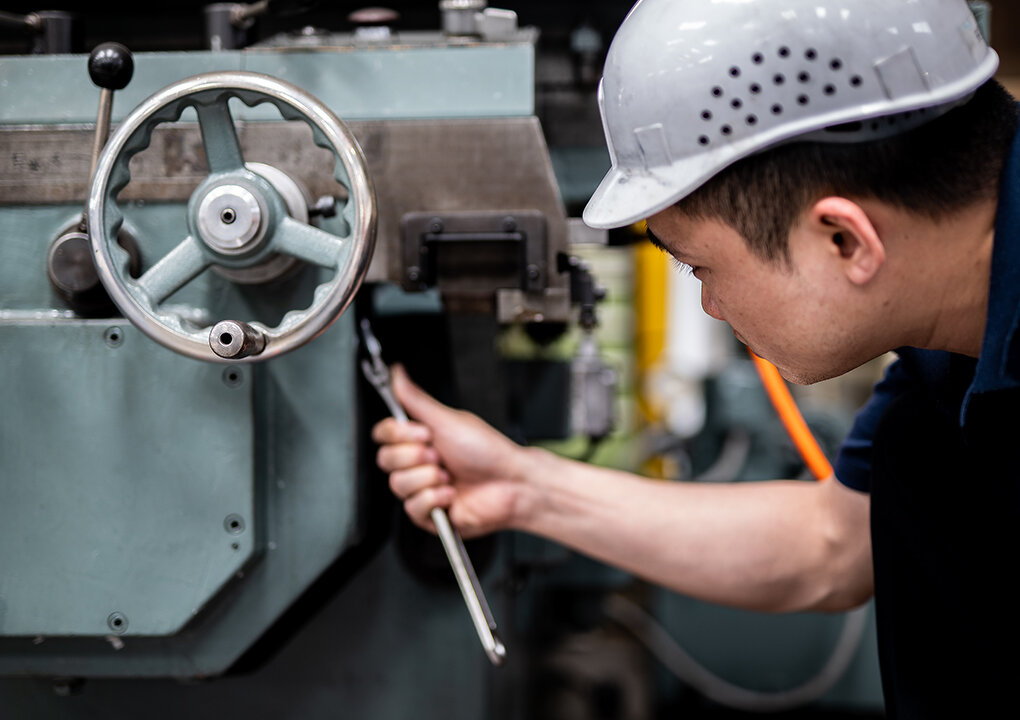
Do you have any of these problems?
- The failure was addressed after it occurred, but it took longer than expected to recover due to delays in procurement of parts, etc.
- The machine is old but left unrepaired. Actually, we don't even know what to do.
- A small faulty part of the machine has spread to other parts of the machine, and it has become unmanageable.
- We would like to do maintenace, but If possible, we would like it to be done when production is stopped.
- Due to lack of human resources, maintenance cannot be carried out in-house.
- We want to repair machines from a foreign manufacturer, but don't know what to do.
- We want to relocate our existing machines overseas, but the manufacturer has refused to deal with our request, so we are looking for a company that can relocate and install the machines.
We can help prevent machine breakdowns and help prevent sales declines.
- We propose and implement periodic maintenance to customers before machine failure/line stoppage
- Our engineers, trusted by major automotive and machine tool manufacturers, will check your machine directly.
- Our excellent quality of maintenance is world renowned, and we have many achievements overseas.
Our maintenance quality has been proven by major automobile manufacturers, contributing to improved productivity and reduced material losses by avoiding downtime.
In preventive maintenance, machine parts are checked and replaced on a regular basis.
By doing so, it is possible to reduce the occurrence of defective products and prevent prolonged stoppage of machines (known as "doka-tei") which could be caused by the late delivery of parts.
Our approach to and quality of maintenance has been accepted by major automobile manufacturers. We also provide maintenance services for the machining lines and respective machines at the plants of major automakers. Furthermore, Shiozawa Kogyo provides maintenance not only to domestic customers but also to overseas plants by traveling to their plants.
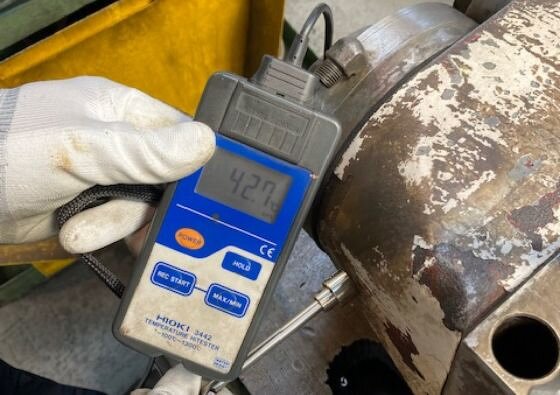
We create a safe and secure work environment where sudden problems can be avoided.
Many quality issues are caused by production line problems. However, if maintenance is performed after a breakdown (after-the-fact maintenance), quality cannot be guaranteed because it is not known when the machine will stop. Shiozawa Kogyo's maintenance team delivers peace of mind through maintenance so that our customers can always work in a stable condition.
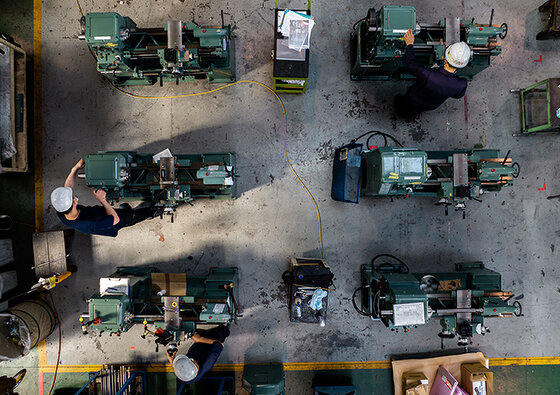
Our thorough PDCA (Plan-Do-Check-Act) approach to maintenance helps reduce man-hours and parts replacement costs.
Shiozawa Kogyo also offers suggestions on the timing and items for periodic inspections. While it is of course important to periodically inspect and repair machines, it is also important to periodically review the evaluation criteria for parts replacement and replacement standards in order to maintain accuracy and reduce part replacement costs. We do not only inspect and repair machines, but also strive to contribute to our customers' business development and credit building.
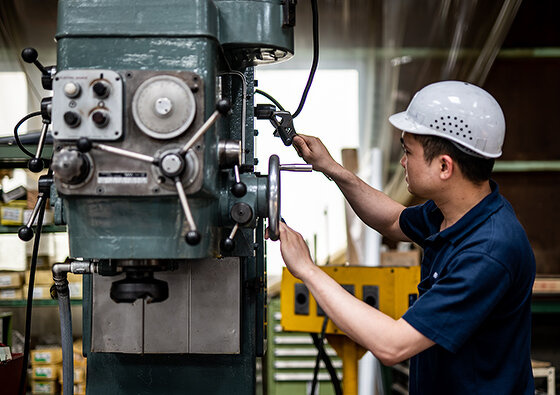
Maintenance and preventive maintenance
We perform periodic inspections and preventive maintenance on behalf of our customers. We can also repair malfunctioning machines on your behalf.
-
1 ) Inquiries
Please contact us first.
Please inform us of the maker, model, type, and date of manufacture of the machine subject to maintenance and preventive maintenance. -
2 ) On-site inspection and meeting
On-site inspection and meeting for maintenance and preventive maintenance If the subject is a line or complex machine, our engineers will make a preliminary inspection of the current status of the subject machine. For on-site start-up support: after a preliminary inspection of the subject machines and confirmation of the precautions to be taken, we will discuss the details of the work and submit a quotation.
-
3 ) Maintenance and preventive maintenance
Confirmation of maintenance intervals and maintenance items & work procedures
-
4 ) Business Meeting
Meeting after submission of quotation
-
5 ) Inspection
Confirmation and implementation of inspection date
-
6 ) Implementation report
We make an implementation report and explain it to the customer.
We will summarize in the report the location of the inspected machine defects and whether or not any parts need to be replaced, and discuss over the issues with the customer. -
7 ) Parts replacement and repair
If parts replacement or repair is necessary, the timing will be set after discussion with the customer, again taking into account the parts delivery date.
-
8 ) Repair implementation and reporting
If repairs are to be made again, we will report on the repairs upon completion and submit a written report of the repairs.